Modular can make a difference – I’ve seen it
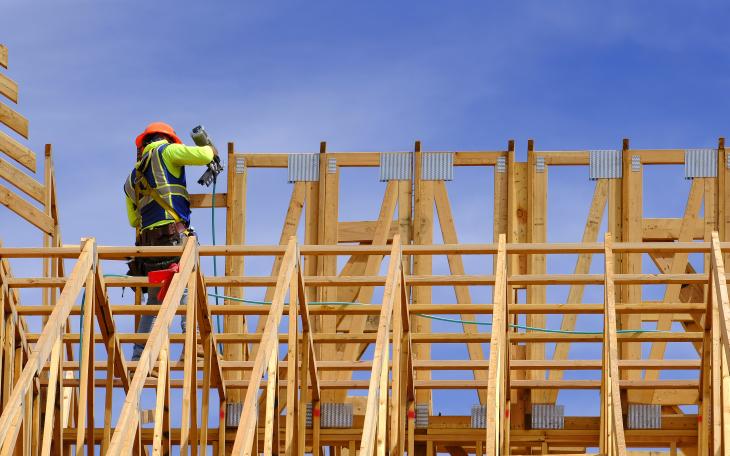
It’s not been a great time for modular methods of construction (MMC). The collapse of Ilke Homes last summer, once the darling of the fledging sector, was preceded by Legal & General’s decision to walk away from its factory in Yorkshire with £100m in losses.
Those events were both well before the Built Environment Committee last month published its own damning assessment of modular take up - “…the Government’s approach to MMC is in disarray. Millions of pounds of public money have been invested, but the money has not been backed by a coherent strategy and set of measurable objectives…” – yikes.
The week after the Committee’s findings were published, I was in Leicestershire standing in a vast factory bigger than five football pitches, watching precision machines punch out timber frame panels in mere minutes. Supervised by just a few operatives working silently, the efficiency of the production line was hypnotic.
This was, of course, a factory pre-manufacturing 2D structural systems (open-panel, timber frames) known as Category 2 delivery – significantly different to the fully modular production (Category 1) that the Built Environment Committee criticised so strongly.
For the first time, major housebuilders are starting to reap the rewards of Category 2 production - Vistry Group is leading the charge via its three modular factories, which combined have the capacity to deliver over 7000 homes a year, whilst Barratt has invested significantly into its own timber frame business.
The efficiencies of Category 2 pre-manufacturing are plain to see, quite literally. But one of the less visible benefits of manufacturing this way is the vast environmental impact it has through a significant reduction in carbon emissions.
There’s no doubt that the industry is not ready to fully embrace Category 1 production – and serious doubts remain that it ever will be – but we should not be so quick to write off other forms of production, particularly as housebuilders work toward 2025’s Future Homes Standard which aims to decarbonise new homes by focusing on improving heating, hot water systems, and reducing heat waste, further increasing the need to build efficiently and sustainably.